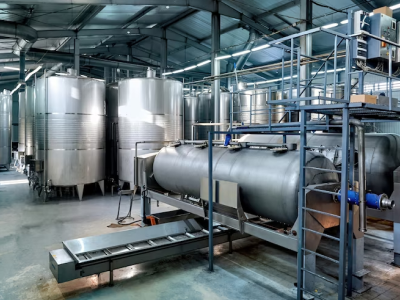
Efficiency is of the most importance in industrial processes. In manufacturing
companies and agricultural facilities, optimizing material handling is important
in increasing productivity and reducing operating costs. The screw conveyor is
one of the most versatile, efficient and reliable mechanisms used for the
transport of material. Optimizing screw conveyor performance in diverse
applications requires an understanding of the basic principles of screw
conveyor design.
Introduction to Screw Conveyors:
Screw conveyors, also known as auger conveyors are mechanisms designed for
the bulk handling of materials, ranging from powders to granular substances
and even semi-solid materials. Their operation relies on the principle of a
rotating helical screw blade within a cylindrical casing. As the screw rotates, it
effectively moves materials along the conveyor’s length, pushing them forward
or upward, depending on the configuration.
Key Components of Screw Conveyors:
Screw Shaft: The central component of a screw conveyor, the screw shaft, is
responsible for driving material movement. It typically consists of a helical
flight wrapped around a central core, providing the necessary propulsion for
material transport.
Casing: Surrounding the screw shaft, the casing forms the enclosure through
which materials are conveyed. It prevents spillage, contains material flow,
provides structural integrity to the conveyor system.
Hanger Bearings: Positioned at intervals along the conveyor length, hanger
bearings support the screw shaft, ensuring smooth rotation and minimizing
frictional losses. Proper selection and placement of hanger bearings is critical
for maintaining conveyor efficiency.
Inlet and Outlet: Screw conveyors feature inlet and outlet sections where
materials enter and exit the system, respectively. These sections are designed
to facilitate the seamless transfer of materials onto off the conveyor,
minimizing spillage ensuring uniform flow.
Design Considerations for Optimization:
Material Characteristics: One of the primary factors influencing screw conveyor
design is the nature of the materials being transported. Factors such as particle
size, density, flowability abrasiveness must be carefully considered to
determine the optimal screw configuration, pitch, speed.
Conveyor Configuration: Screw conveyors come in various configurations,
including horizontal, inclined and vertical orientations. The selection of the
appropriate configuration depends on factors such as space constraints,
material flow requirements and process dynamics.
Screw Geometry: The geometry of the screw, including its diameter, pitch and
flight type, significantly impacts conveyor performance. Larger diameter screws
with greater pitch provide higher throughput but may require more power.
Conversely, smaller screws offer enhanced precision but may be limited in
capacity.
Operating Conditions: Environmental factors such as temperature, humidity
and exposure to corrosive substances can affect the performance and longevity
of screw conveyors. Proper material selection, surface treatments and
protective measures are essential for ensuring durability and reliability under
varying operating conditions.
Benefits of an Optimized Screw Conveyor Design:
Increased Efficiency: A well-designed screw conveyor can significantly improve
material handling efficiency, reducing processing times and enhancing overall
productivity. By minimizing material spillage, clogging, downtime,
optimized conveyors contribute to smoother operations and higher
throughput.
Cost Savings: Optimization of screw conveyor design can lead to substantial
cost savings over the long term. By reducing energy consumption, minimizing
maintenance requirements and extending equipment lifespan, businesses can
achieve significant returns on investment and improve their competitive edge.
Enhanced Safety: Properly designed screw conveyors prioritize safety by
minimizing the risk of accidents, spills, equipment failures. Operators can
mitigate potential hazards and ensure a secure working environment by
incorporating safety features such as guards, emergency stops, overload
protection systems.
Versatility and Adaptability: Screw conveyors are highly versatile systems that
can be customized to suit a wide range of applications and operating
conditions. Optimized conveyors offer flexibility and adaptability to meet
diverse industry needs, whether handling bulk solids, slurries or hazardous
materials.
Conclusion:
By understanding the key components, design considerations and benefits
associated with screw conveyors, engineers and operators can enhance
efficiency, reduce costs and improve overall performance. As industries
continue to evolve and innovate, the importance of optimized conveyor design
remains paramount to driving progress and sustainability.